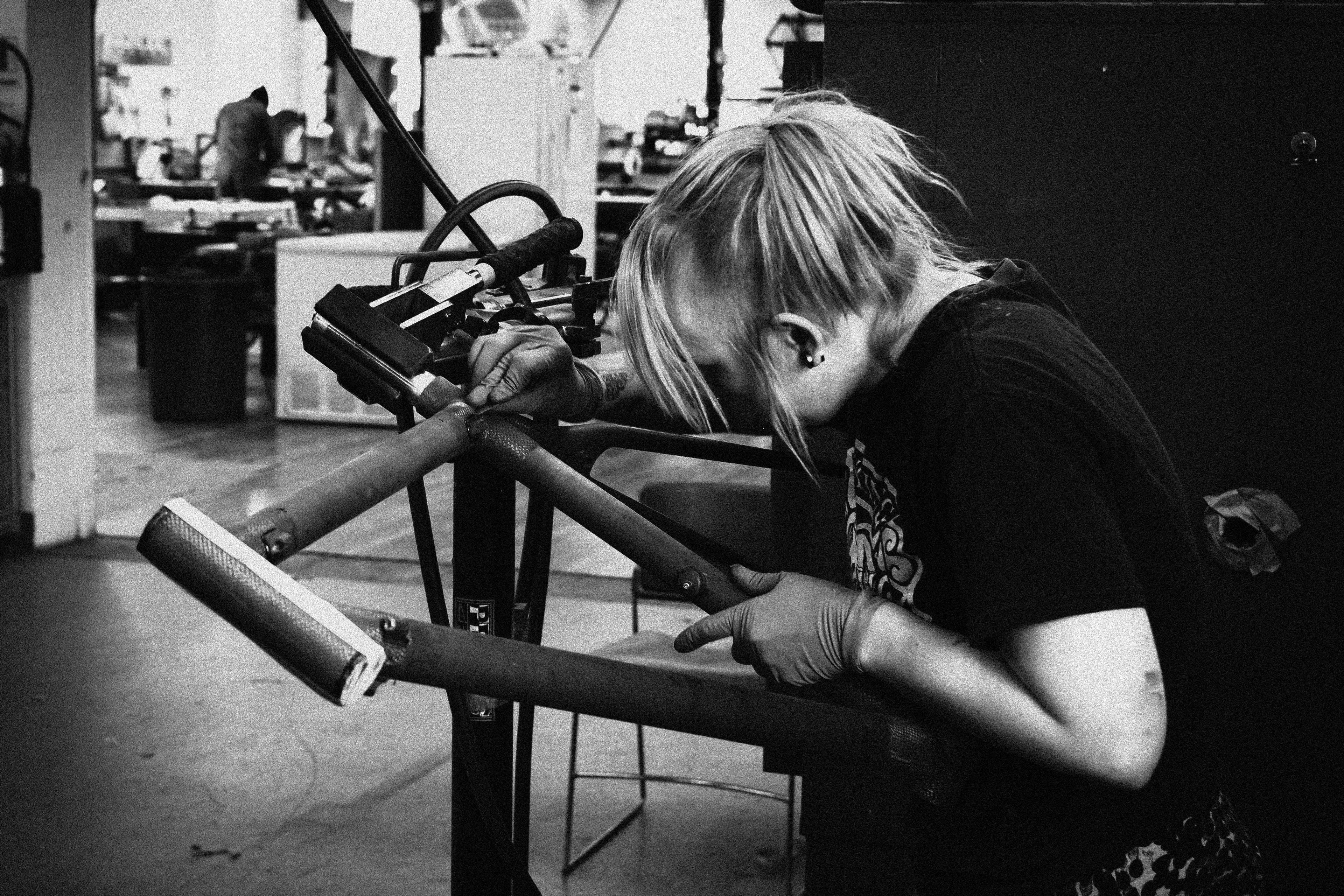
Parlee Custom Series
YOU DREAM IT, WE BUILD IT
For over twenty years, our unwavering mission remains the same: Build the best performing bike possible. Period.
One way to guarantee that a bike will perform perfectly is to have the bike custom-made for you. Our Z-Zero models are each perfectly designed and built for one person: you.
Attaining the ultimate in custom performance is accomplished through a combination of masterful design, unwavering attention to detail, and total pride in the finished product. Bob wouldn’t do things any other way, and that’s why his name — and reputation — is attached to every single bike we build.
Parlee’s unmatched customization ability is the end result of a multi-tiered process that begins with one simple edict: listen. Parlee understands that the most important aspect of the custom bike-building process is communication between the rider, the fitter, and us, the builder.
If you’re considering a custom bike, call us. We are always happy to explain how our custom bike-building process works so well. We work with the finest retail and fitting partners around the world using a highly-refined design process that ensures perfection.
Collapsible content
Fit
Is it possible to have a modern, high-performance carbon bicycle that is also perfectly fitted to your unique needs?
Yes, it is and Parlee is a pioneer in this field. Our special molding process, allows us to alter frame geometry by as little as 0.1-degree of angularly and one millimeter linearly. This allows us to accommodate virtually all riders and riding styles.
Full custom fitted geometry is available on our Z-Zero, Z-Zero Disc, Z-Zero XD (CX, Gravel or Commuter spec) platforms. All custom designs are created using our proprietary Computer-Aided-Design system, which models you unique contact points and aligns them with actual frame geometry to assure a flawless finished product.
Feel
Consider the adjectives that describe a bike: quick, stiff, smooth, comfortable, responsive or stable. Each is subjective, resulting from that bike’s tube diameter, tube length, fiber composition, fiber orientation, and angular permutations. Understanding the delicate dance of these variable characteristics is knowledge only attained through years of hands-on observation and practical experience building bicycles.
For over two decades, Parlee has built customized carbon fiber bicycles, for a very broad spectrum of riders, from well-known professionals to enthusiastic amateurs. From these experiences, we have the knowledge, data, and skill to precisely tune each Z-series bicycle to your individual needs. This is a marked departure from standard industry practice, where bikes are designed based on the law of averages. A Z-series, precisely built for you, will be anything but average.
All Z-series tubes are custom blended (at no extra charge) on all made to order Z-series bicycles to perfectly meet each riders needs. The gorgeous carbon tubes and frame parts are all made by hand, in house, here in Beverly, MA by our frame building team to Bob’s exacting designs.
Components
Parlee and our dealers offer high-end Shimano, Campagnolo and SRAM build kits, plus componentry from ZIPP, HED, Mavic, ENVE, and other bike part manufacturers. If you can dream it, we and our retail partners can build it.
Details
Unlike the bike-building behemoths, Parlee is a nimble operation, capable of creating a bike that meets your exact wants and needs. Parlee can customize a vast range of fittings and interfaces. Options include English bottom bracket threading, or our open industry standard Press-Fit 30 designs. Parlee can also modify cable stop placement, route Di2 or EPS internally, build eTap frames with no drillings and add eyelets, pump pegs and bottle mounts. Racks, fenders, power meter sensors and other mounts are all options.
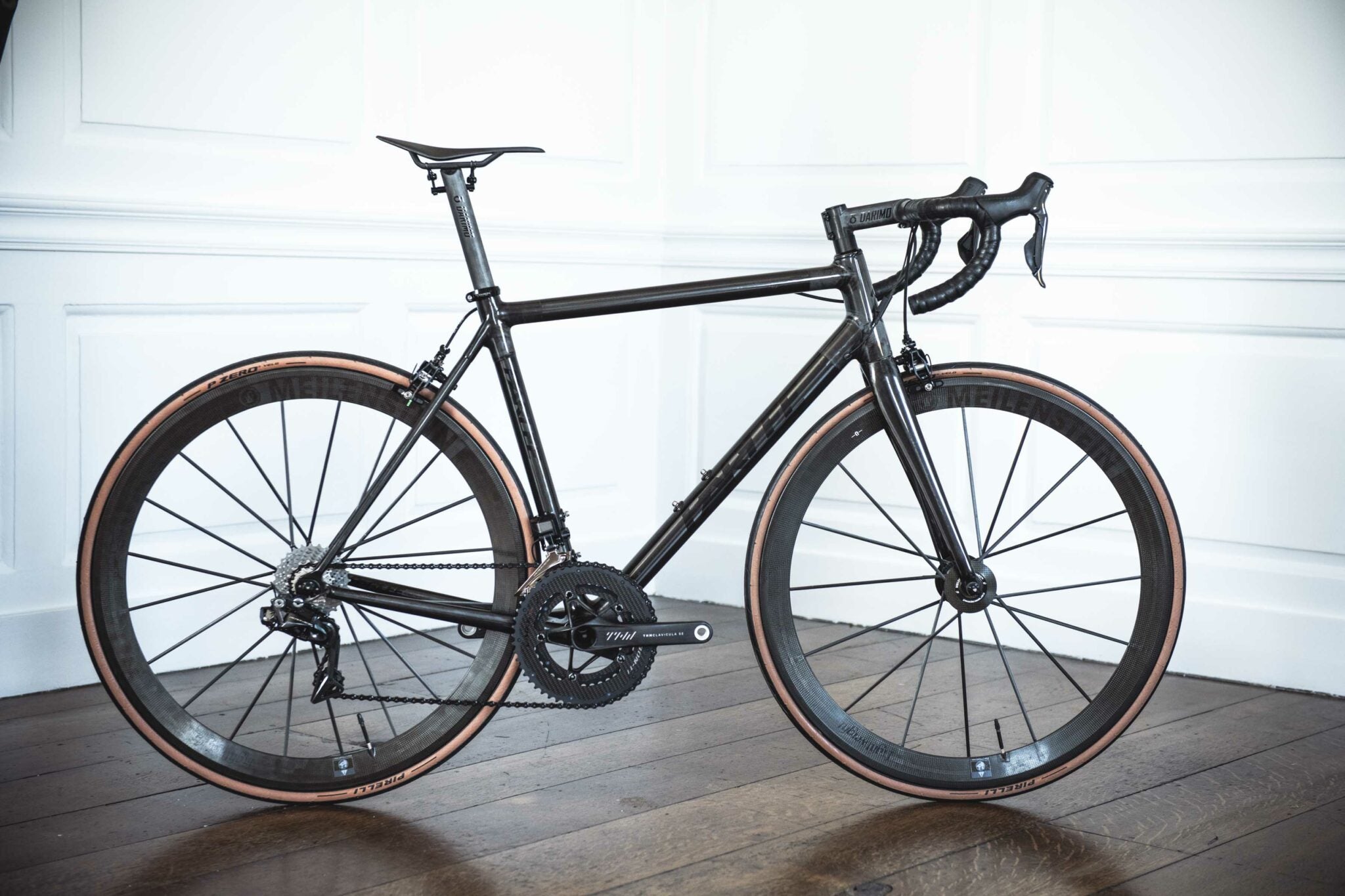
Parlee Z-Zero
5.5kgs, IMAGINED BY THE BIKE TAILOR
The Parlee Custom Process
-
1: Building the Blueprint
It all starts at an authorized Parlee dealer, where a trained technician takes precise measurements and gathers all the essential customer information. This information is then delivered to Parlee’s state-of-the-art Massachusetts headquarters, where we use custom CAD software to create the blueprint of your perfect bike. Before a single tube is built, we send you a document to double-check every detail.
-
2: Custom Carbon Fiber
Every Parlee frame starts with high-modulus, uni-directional carbon fiber tubing. These tubes and sub-assemblies are produced exclusively by Parlee, and each one is meticulously inspected, then mitered to size. After the ends are cleaned and media-blasted, the tubes are inspected again. The goal is to create the perfect surface to work with, which is critical to long-term durability. This process is one reason that Parlee frames are backed by a lifetime warranty.
-
3: Construction & Assembly
These custom carbon tubes are then selected and assembled based on a customer’s desired ride qualities. We use specially designed jigs that are accurate to sub-1mm tolerances. Each lug is mated by hand around the mitered tubes, which allows us to customize the stiffness level. Correct fiber orientation is key to frame strength and ride quality.
-
4: Molding
Frames are put through a proprietary heating and pressurization process that creates an unbreakable bond. This proprietary molding process ensures a consistent surface finish.
-
5: Raw Finishing
Next, frames are hand-sanded and cleaned before small parts are installed. All of our carbon fittings such as cable stops and front derailleur mounts are made in-house. This helps us achieve the lightest, strongest connections between the frame and its components.
-
6: Paint & Final Prep
When it comes to paint, Parlee customers have unlimited color choices. After each frame is assembled, it goes through an exhaustive wet-sanding process, where progressively finer grit paper is used to produce a mirror-like shine. Once the final paint is applied, the total build time for each frame is about 40 hours, up to four times longer than that of the average custom bike. Our average delivery time is about 30-45 days.
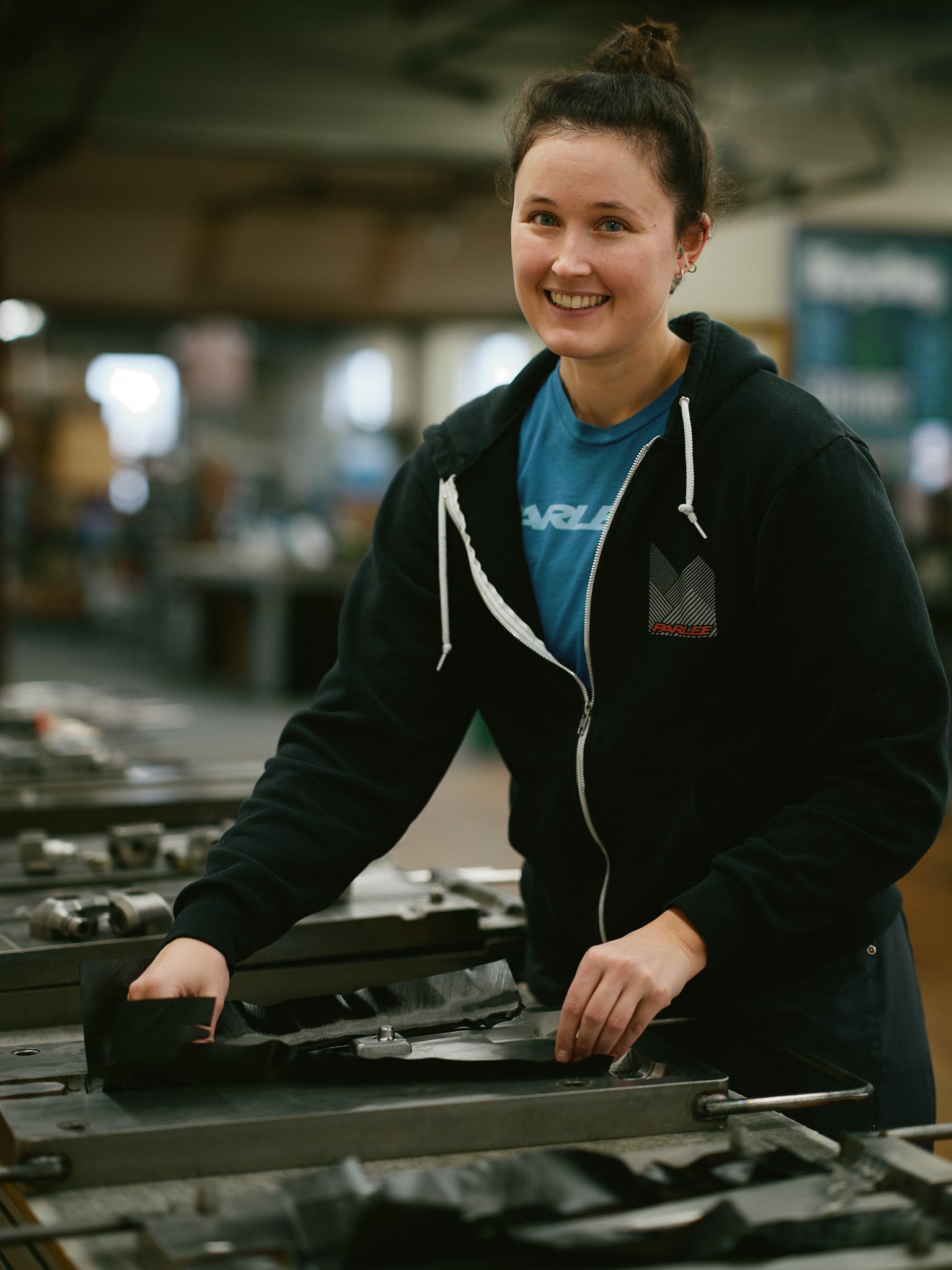
Lyndall
Custom Fabricator Manager
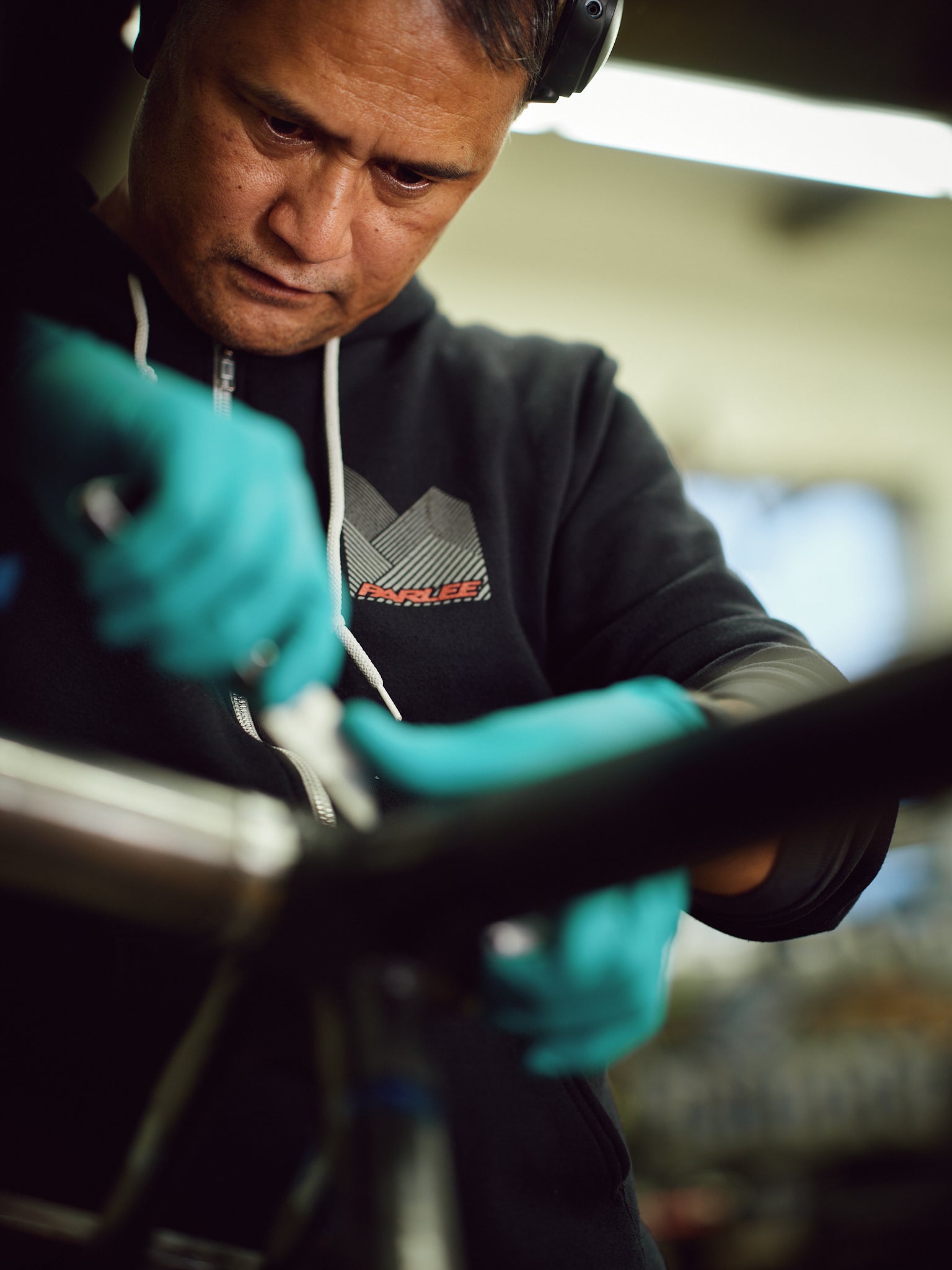
Rommel
Lead Frame Builder
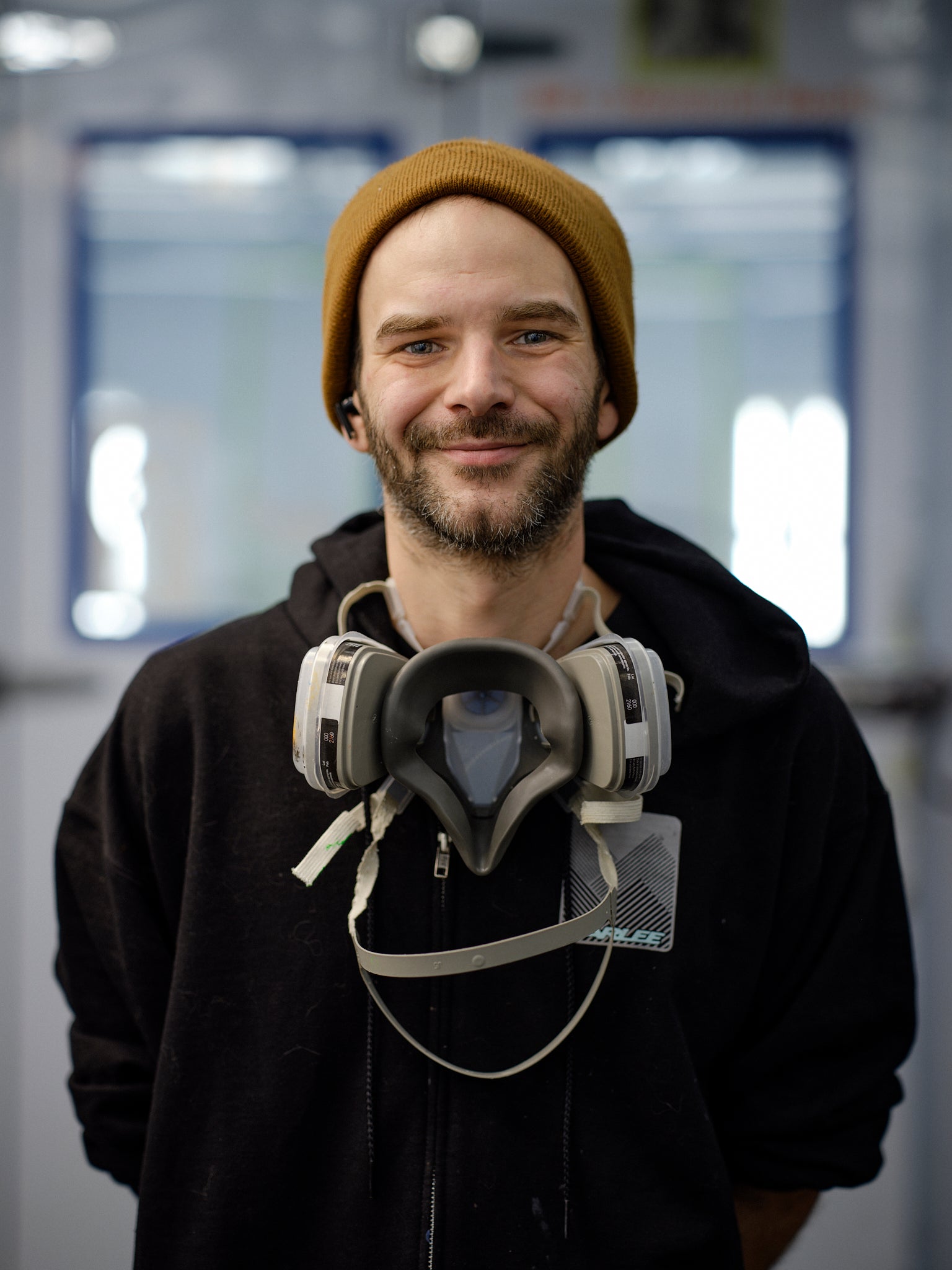
Cody
Paint Expert
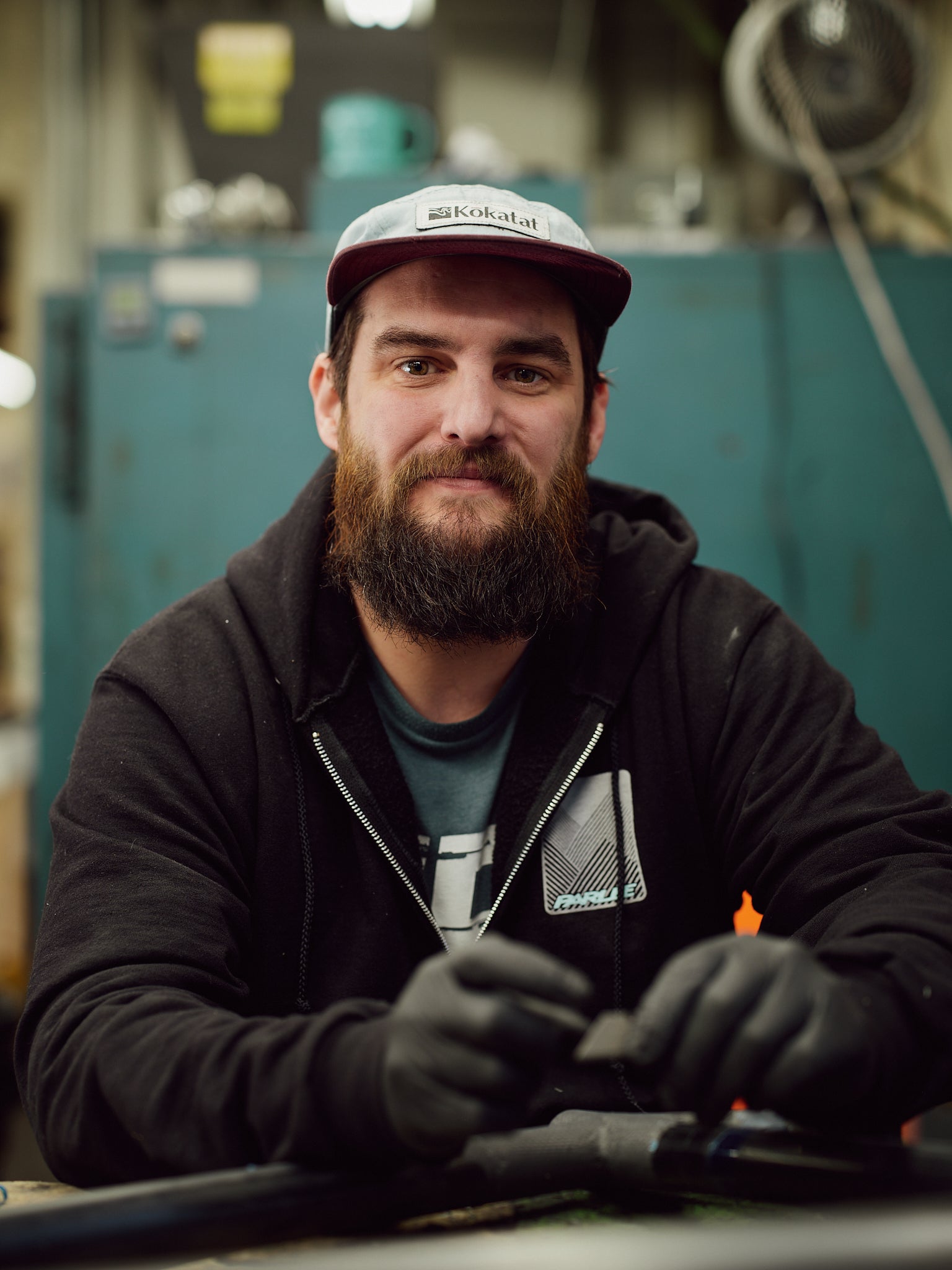
Corey
Custom Fabricator
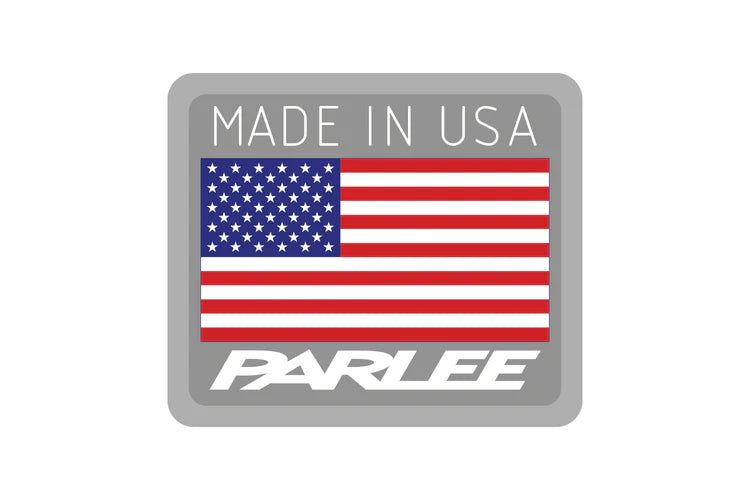
Made in the USA
Every Parlee Z-Zero is made in our state-of-the-art facility in Beverly, MA.